Creep Testing at TCR Engineering
- Rohit Bafna
- May 16, 2018
- 2 min read
TCR in its materials testing laboratory in Mumbai, India has multiple creep testing machines which assess how materials behave under long-term exposure to stress and elevated temperatures. This form of testing is essential for industries where materials are expected to withstand prolonged mechanical stress without failure, such as in power generation, aerospace, oil and gas, and structural engineering.
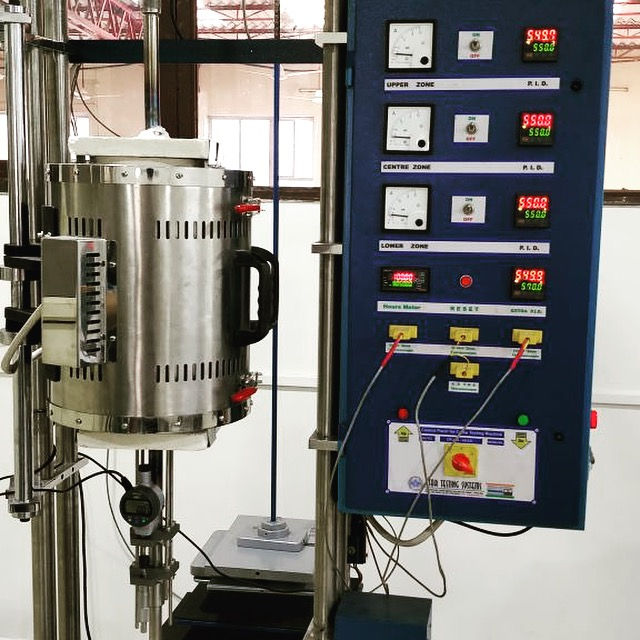
Creep refers to the slow, progressive deformation of a material when subjected to a constant load or stress, typically at high temperatures. Unlike sudden failures such as fracture or fatigue, creep occurs gradually over time and can lead to serious failures if not properly accounted for during design and material selection.
Materials that are subjected to high temperatures and constant stress, such as components in gas turbines, boiler tubes, or pressure vessels, are highly susceptible to creep. Conducting creep tests ensures that these materials will maintain their mechanical integrity over time, reducing the risk of unexpected failure and extending the operational life of components.
In a creep test, a sample material is subjected to a constant load (or stress) at an elevated temperature over an extended period. The test measures the strain (deformation) experienced by the material and plots the strain vs. time curve to observe the material’s performance over time.
Key variables in creep testing include:
Stress: The force applied to the material.
Temperature: The elevated temperature at which the material is tested, often mimicking real-life operational conditions.
Time: The duration of the test, which can range from hours to several months or years.
The resulting data provides critical insight into the material’s ability to resist creep, allowing engineers to predict the long-term behavior of materials and components.
Applications of Creep Testing
Aerospace Industry: To ensure that engine components and airframes maintain their strength and structural integrity over time despite exposure to high heat and stress.
Power Generation: Boilers, turbines, and nuclear reactor components need to withstand extreme conditions without deforming, which could cause operational failures.
Oil and Gas: Pressure vessels, pipelines, and refinery equipment must endure high temperatures and stresses over long periods, making creep testing essential for safety and reliability.
Creep testing is essential for predicting the long-term performance of materials used in critical applications. It ensures that components can handle the rigors of extreme environments and prolonged stress, ultimately enhancing safety, reliability, and efficiency across industries.